Although all self-dumping hoppers serve the same purpose—streamlining material handling and waste management, they can be categorized into different types based on their design and intended application. From heavy-duty models built for industrial scrap to lightweight hoppers for recyclables, each type offers unique benefits.
Let’s explore some of these different types!
Forward-Dumping
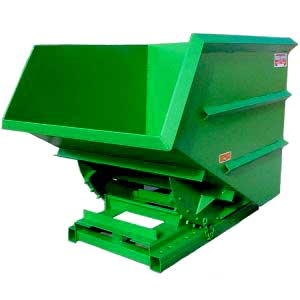
Most of Roura’s hoppers fall into the “forward-dumping” category, meaning they’re designed to tilt forward when released. Forward-dumping hoppers can be further categorized by the material they’re constructed from and their size.
Benefits
- Reduces the risk of spills and accidents.
- Available in different sizes, load capacities, and material types to meet different operational needs.
- Keeps weight evenly distributed without the risk of tipping.
- Require less clearance on the sides, so they’re great for confined spaces.
Best Applications
- Collecting and transporting dense scrap, raw materials, and production waste in manufacturing processes.
- Handling concrete and other heavy construction debris.
- Sorting and disposing of large volumes of recyclable materials.
- Forklift operations where forklift access is only available from the front.
90-Degree
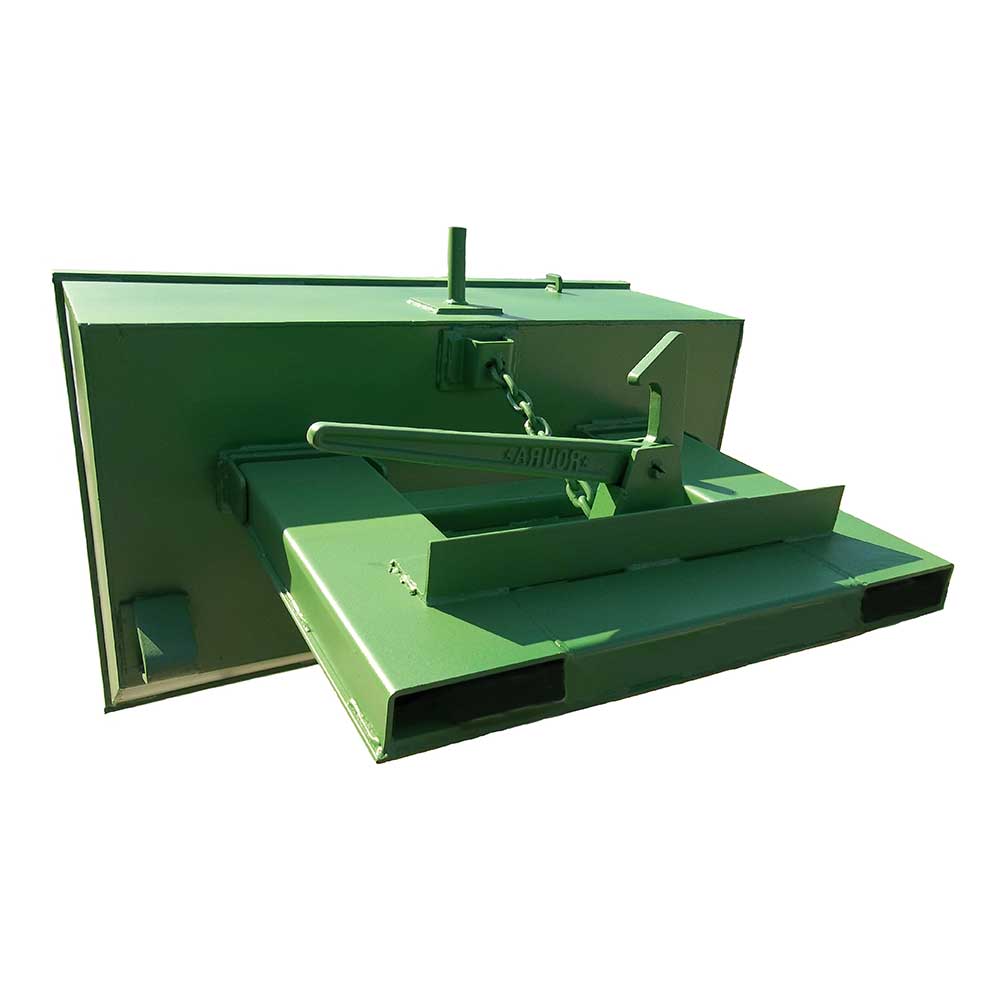
90-degree self-dumping hoppers are a unique, Roura-exclusive design. They are technically a type of forward-dumping hopper but with a low standard. As the name implies, it empties materials at a 90-degree angle. Once the hopper is lowered to the ground, it automatically returns to its upright and locked position.
Benefits
- Ensures full material discharge.
- Can handle materials that may cling to the hopper’s interior (like sawdust and wood shavings).
- Can be used with forklifts or other lifting equipment, providing better flexibility when used on different job sites.
Best Application
- Collecting metal chips, shavings, turnings, and sawdust debris.
Dross

Similar to the 90-degree hopper, a Dross hopper is a type of forward-dumping hopper with a unique design. It’s made from heavy-duty steel that can withstand extreme heat and features a double wall construction, a 3/8” plate liner, and 1/4” perforated sidewalls. This design allows for quick heat release, so it’s primarily used to handle extremely hot materials.
Benefits
- Can withstand extreme temperatures from molten metal and slag.
- Reduces the risk of spills and accidents.
- Will resist warping, cracking, and other damage over time.
Best Applications
- Collecting and transporting aluminum, steel, and other metal dross.
- Handling slag and other byproducts of high-heat metalworking processes.
Dewatering
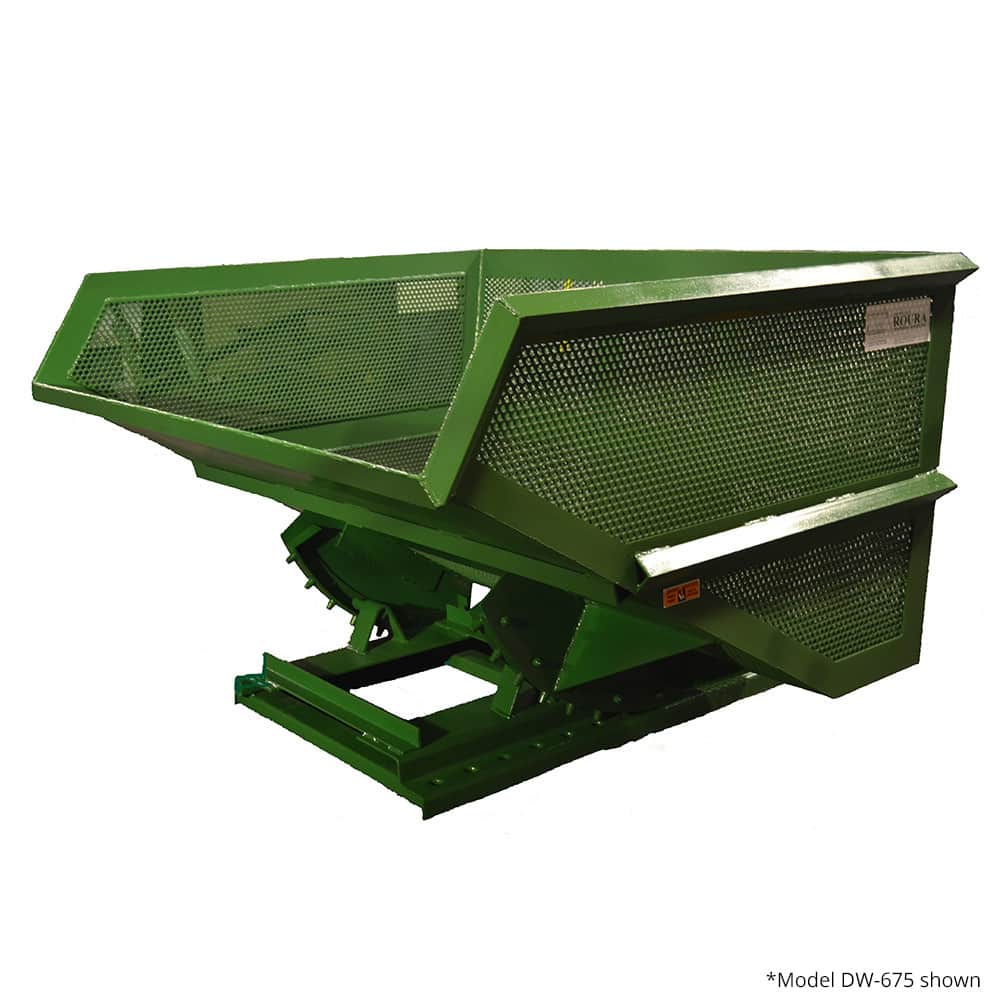
Dewatering hoppers, also forward-dumping, are specially designed for wet material applications, such as pulp processing. They’re made from carbon steel and feature perforated sidewalls that help contain solids while releasing extra liquid.
Benefits
- Helps reduce waste volume and disposal costs by separating excess liquid.
- Made with corrosion-resistant components to ensure optimal performance for many years.
- Makes transportation of wet materials safer and all around more efficient.
Applications
- Managing wet waste, food scraps, or industrial sludge.
- Collecting and transporting wet debris.
- Separating oils and liquids from solids.
- Drains organic waste, pulp, and other food and beverage byproducts.
With Lid
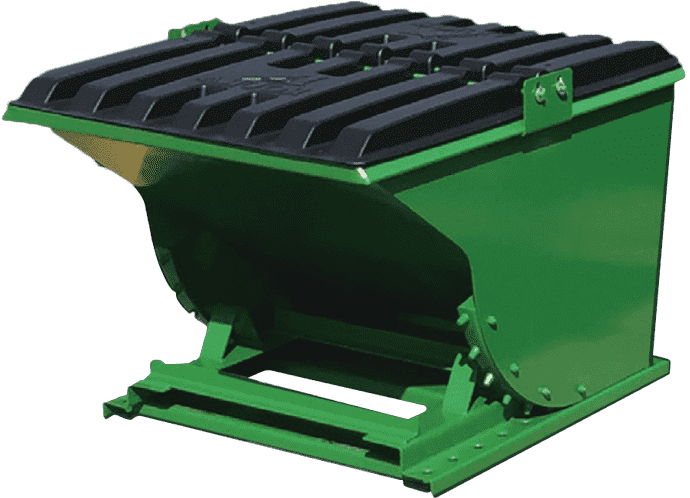
Hoppers with lids are just traditional forward-dumping hoppers with an added lid for extra security and protection. These lids can be made from metal or plastic and help prevent spills, control odors, and protect sensitive materials.
Benefits
- Great for indoor and outdoor applications.
- Reduces mess in work areas by preventing potential spills.
- Shields materials from the rain, wind, and snow.
- Reduces risk of exposure to hazardous or other dangerous materials.
- Controls odors (especially with refuse).
- Prevents animals or insects from accessing the hopper.
Best Applications
- Containing lightweight recyclables that could be blown away.
- Securing sensitive materials and chemicals.
- Storing organic waste, refuse, and other odorous materials.
Lined

Lined hoppers are also primarily forward-dumping but feature interior linings made from polyethylene, rubber, or steel to prevent damage to delicate or abrasive materials or protect the hopper itself if corrosive materials are being stored in it.
Benefits
- Prevent residue buildup when handling sticky or fine materials.
- Provides a cushioned interior for fragile or delicate materials.
- Dampens noise when handling metal, glass, and other hard materials.
- Provides chemical resistance for hazardous material handling.
Best Applications
- Handling metal scraps and sharp materials.
- Transporting fine materials that can build up easily.
- Hauling organic materials.
- Transporting corrosive materials.
Bottom-Release

Bottom-release hoppers, like Roura’s bottom drop boxes, empty contents through a trap door mechanism at the base rather than tilting forward or sideways, so they’re commonly used to discharge bulk materials into chutes or underground pits.
Benefits
- Allows for measured discharge.
- Reduces impact and dust.
- Great for heavy, dense materials.
Best Applications
- Handling sand, gravel, metal shavings, and other compact materials that don’t slide out easily.
- Any material handling operation that requires materials to be dropped onto conveyors, sorting stations, or mixing systems.
- Applications that require materials to be disposed of in storage bins or underground collection pits.
- Controlled discharge of grains, feed, and bulk agricultural products.
Open-Side
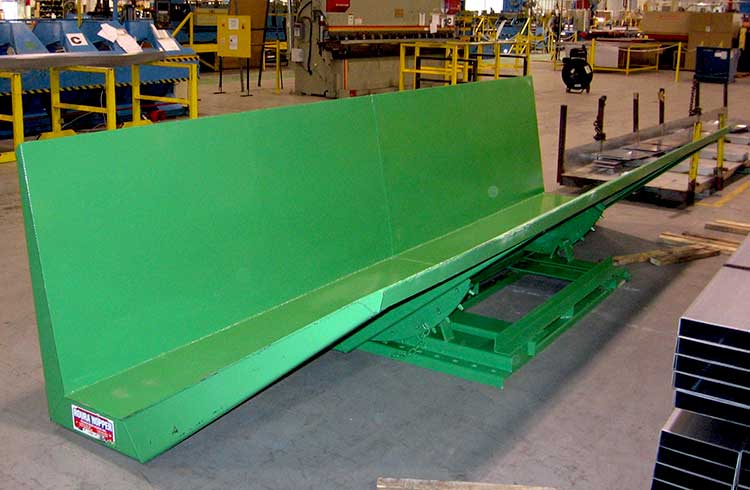
As the name implies, open-side hoppers have one or more open sides for easy loading of oversized or irregularly shaped materials that are difficult to transport, such as wooden planks or sheet metal.
Benefits
- Provides unrestricted access.
- Allows for faster and easier loading and unloading.
- Handles items that don’t fit in traditional self-dumping hoppers.
- Works for both manual loading and forklift-assisted operations.
- Doesn’t require breaking down the materials beforehand.
Best Applications
- Collecting long, bulky materials.
- Storing and moving large industrial scraps or byproducts.
- Handling lumber, rebar, or other large construction debris.
Skeleton
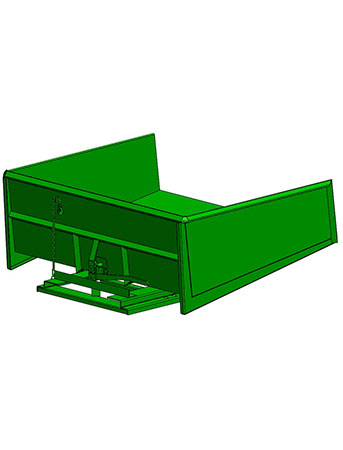
Skeleton hoppers are similar to open-side models but have a slightly different design. While open-side hoppers are primarily used for long, irregularly shaped materials like wood and rebar, skeleton hoppers are wider with one open end, so they are good for handling flat, wide materials like sheet metal.
Benefits
- Unrestricted access from one side.
- Keeps materials organized and easily accessible.
- Heavy-duty design to handle larger loads.
Best Applications
- Transporting sheet metal.
- Use with sheet metal processing equipment.
Find the Right Hopper Today
Not all hoppers are made the same. If you’re not sure which hopper is best for your application, please visit our Buyers’ Guide or contact us today to speak directly with one of our experts!